Can Robotics Save Shipbuilding?
Not since the first steam ship set sail, have shipbuilding evolved with the times. Now ships are not just made larger and sturdier, they also now represent the new face of what the industry is poised to herald. Jaya Prakash reports.
As it can be clearly imagined shipbuilding is a complex process explaining why the industry is only monopolised by a few nations in the world.
Right from the time naval architects begin designing vessels, to procurement and processing of material, hull construction, the installation and testing of sophisticated control such as the funnel and propellers and propulsion systems, with enormous steel structures it is without the slightest bit of doubt, a ‘painfully’ long and drawn-out process. The actual building of a ship depends on the yard and that yard’s specialty and its expertise in vessel types.
It is a given that yards, use construction technique with unit sizes that are determined by the capability and capacity of available handling and other equipment. The units come from flat plates and sections cut to size and welded together to form a variety of sub-assemblies and assemblies, which are subsequently joined together. Outfitting is where most of the labour-intensive stage of the process is using a while suite of tradesmen.
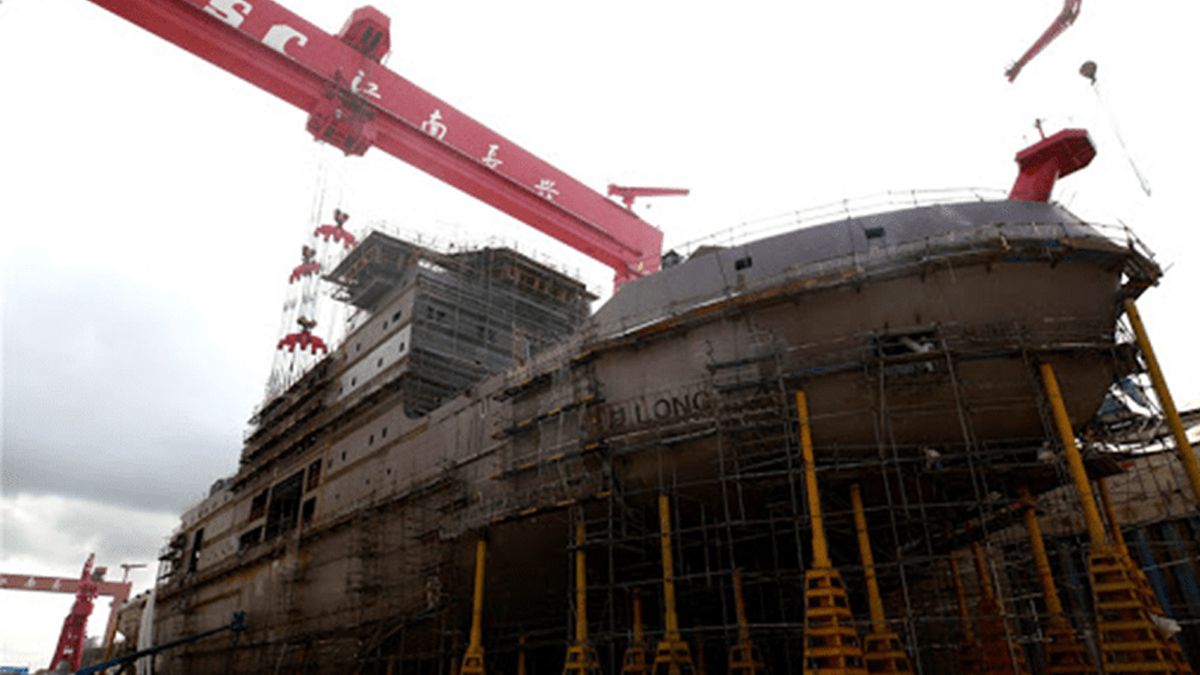
Such being what it ordinarily is extracts huge building costs, not to mention manpower. The price of a container ship some ten years ago was USD10million, whilst a bulk carrier can cost something beyond USD25million in today’s prices. It is much more these days, especially when many owners are now seeking hybrid engines. Most of the prices are determined by the price of steel, rudder installations, anchor, bow, keel, propeller etc. Overheads too, exact a heavy price depending on the location of the yard and the price of land that is to be used for shipbuilding.
The use of manpower has without question, been somewhat of a bane for yards grappling with building costs. Cost is not the only determinant. Specialised skill is rare, few and far between and that means just only selected individuals from specific nations can be hired. All of these is over and above bureaucratic tangles yard owners need to confront with authorities.
Unions and constant haggling for wages in parts of Korea, Japan Greece, and Turkey, have naturally been an unwelcome bugbear in the total matrix of shipbuilding; all because they add to costs. That just explains why technology has been all the rage. Just in ceramic welding alone, especially on shell platings and block connections, it becomes easy for welders effectively shortening the production period. Now yards aiming for bigger vessels use robots for welding. This increases quality, production capacity and decreases the planning times and production periods.
Slowly but surely, shipbuilding is evolving, and technology is the reason for it along with cost pressures.
Clearly, it is in artificial intelligence where the changes have been most profound. In Daewoo Shipbuilding & Marine Engineering in Korea, artificial intelligence for hot processing a robot system that combines technology is applied.
The Korean behemoth has developed an artificial intelligent hot processing robot ’Goknuri’ able to produce high-quality products even with the people employed are not without nominal skills.
The robot ’Goknuri’ works by a process of data storing and using data on techniques. The stored data is then used for the construction of other ships using artificial intelligence technology in the future.
Additionally, it improves the working environment of workers exposed to noise and musculoskeletal diseases. The Korea Herald says it is the AI robot for metalworking in the construction of ships for the first time in the world. The new device is also used to shape steel plates into curved ones at the front and the rear of a steel hull in Daewoo Shipbuilding’s shipyard in Geoje Island, about 400 kilometres south of Seoul, South Korea’s leading shipbuilder said.
Hot working is the metalworking process carried out above 800 C to curve steel plates in the construction of vessels. Hot working requires little force to produce curved surfaces compared to cold working, but it is difficult to uniformly heat the steel plate, so there is a difficulty in having to rely mainly on the experience of a skilled high-tech person to maintain steady quality.
The innovations and experiments do not just stop there. Engineers will, increasingly in the years ahead, use artificial intelligence (AI) to design ships by integrating all kinds of requirements and parameters. Generative design is a design method in which the output, image, sound, architectural models, animation, are generated by a set of rules using a computer program, making it easier to design structures and saving on costs. The digital twin concept will soon be billed as being crucial as it will allow for a full digital replica of a ship to be created and application profiles to be simulated.
Robotic technology is the other ‘big thing’ in shipbuilding. Hyundai Heavy Industries has devised a system that will automatically shape a vessel’s 3D curved surface at its Ulsan yard. In Hyundai’s estimation, it will raise productivity by three times.
Just not to be outclassed is Daewoo, the household name in LNG vessel building. It is using robotics technology to build key sections of container ships. It has been using a 16kg robotic arm to weld parts of its ice-breaking liquefied natural gas carriers. Named ‘Caddy’ by the company, these arms can work on the hull to fuse steel structures together in a confined space.
And it is not just in the shipbuilding alone that automation has come in handy. In Ireland, an unmanned craft is behind the patrolling of sites and to effect repairs to marine renewable energy facilities.
Signs and signals are everywhere that a robot revolution is afoot. The touted Industry 4.0 welds together physical production with smart digital technology and machine learning, to create a better-connected ecosystem for companies. And in the process ignites a robotised production platform, promising greater efficiency, shorter production cycles and a tighter, streamlined performance.
And if oil prices continue to be volatile, there is the possibility that increased automation will help control costs and create a more sustainable business model.
It appears there is no doubting the extent and benefits technology brings to yards.
“Technology is bringing so much of efficiency to yards”, pointed out Arjun Batra, group managing director in Singapore’s Drewry Maritime Services to Marine and Offshore. And that, according to him, results in huge savings for yards, something all builders seek, like the proverbial Holy Grail.
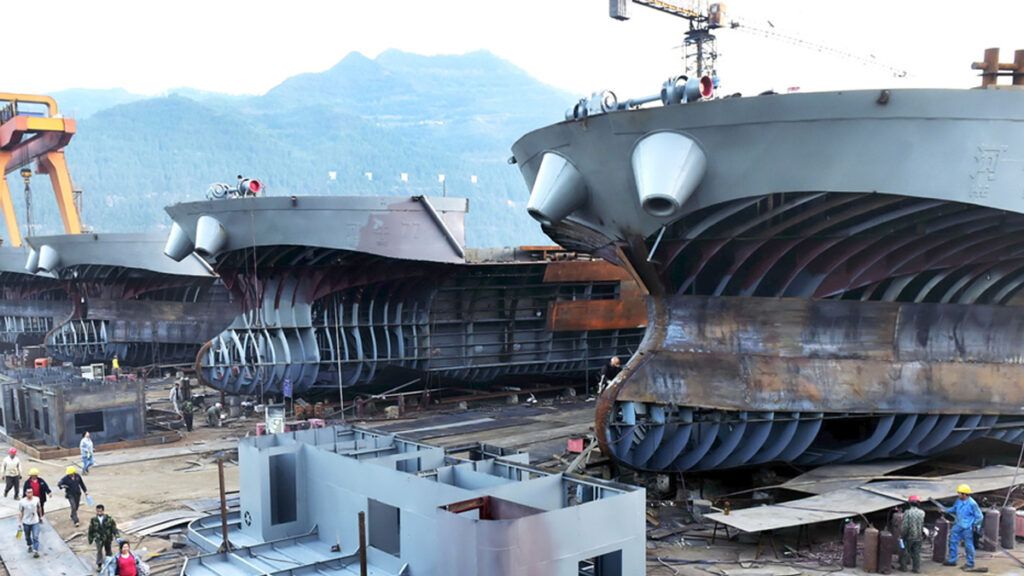
One of the key areas where technology ‘dazzles’, says Batra, is in the conceptual design stage. The ‘ace weapon’ in 3D printing technology, is that it makes possible to construct real objects from virtual 3-D objects. This process is carried out by cutting virtual object in 2-D slices and printing the real one slice by slice.
The other innovation, seen in yards, is where steel cutting and welding have become streamlined that it neatly fits the hull structure and all materials into a single unit.
The advent of technology has certainly projected to be a boon for Japan which has been battling a falling birth rate and reeling under the strains of a labour crunch. It is a phenomenon that Batra characterises as having a ‘stabilising effect’ on the nation.
Just as significant, is the growing popularity of liquefied natural gas (LNG) as an alternate marine fuel. In LNG engines, CO2 emissions are reduced dramatically whilst NOX and SOX, and particulates are almost drained off completely.
Major engine makers are actively pursuing LNG-fuelled engines and classification societies have lined up behind them. And along with it, is the integrated electric propulsion technology which is now making revolutionary waves.
Gas turbines and diesel generators both generate three-phase electricity which in turn power electric motors that turn propellers. A key advantage of that technology is the freedom of where to place the engines, it creates less noise and there is considerable weight reduction.
WILL TECHNOLOGY REALLY BE THE BUZZWORD?
It need not be said, that ships harnessing the right technological mix of emissions control and keen digitalisation contrivances may just steal the day for the yards that built those type of ships!
“Cutting edge propeller design by Japanese yards”, have endeared some Japanese yards to owners, said Nazery Khalid, a maritime analyst from Malaysia. Observed Khalid, the key challenge is if smaller yards and the much bigger and established yards, can all act in unison to embrace the change now underway for yards, from conceptual to detail design.
As can be expected there “will be resistance” explained Rachit Jain, managing director of Safe Lanes Consultancy, within the context of cost and value of the total incorporation of technology. Jain, conceded that shipping is an area where the industry needs to progress, comparing it with aviation and adding of the need to “bridge the gap”. Continued Jain “definitely we (meaning the shipping industry) have to bring in technology”. And technology will also help in fostering safety, he said.
Yet if there is something larger than of all that is unfolding before the world it is just what the International Maritime Organisation (IMO). Right from its double hull ruling to MARPOL rules on sulphur content in fuels, the urgency has been to fit out vessels meeting the carbon challenge.
Zero carbon propulsion vessels are the buzzword but, as is the fragmented nature of shipping and yards, nothing as of now is quite certain if owners could quite afford the very expensive overlay that comes with the ultra-modern ship propulsion systems.
The eventual aim is to have electric ship engines on the back of hybrid ones. And advanced digital systems that give a ‘makeover’ to the present ECDIS and ORCA type of artificial intelligence for navigation may just be what the world yearns for; but they may not be available either for lack of drive to have them implemented because shipping, as was mentioned, is fragmented and disparate, or, they simply they are too expensive.
Then, there is the issue of ‘legacy’ when builders confronted with the idea of having to migrate data may find such an exercise costly. That creates something of a double-edge sword kind of a scenario; that of having the technology but with no skilled expertise to man and manipulate such systems and compelled by force of such circumstances to revisit the old and laborious system that predated the installation of the new!
Fixing requires more money but the temptation to use two systems creates its own challenges. So the talked about robot revolution must have to take a back seat until the fragmented nature of shipping sorts itself out.